Retooling Reduces Down Time, Keeps Revenues Flowing
[This is the fourth in a five-part series of articles expanding on the “equipment equation” for laundromats. In this final installment, we examine another key benefit of replacing older equipment – fewer repairs and lower maintenance costs. Owners of laundromats equipped with new washers and dryers can look forward to spending far less money and time on repairs and parts. And, if repairs do become necessary, newer machines have in-force manufacturer warranties that significantly lower the business’ exposure to those costs. Perhaps most importantly, new machines mean more trouble-free uptime to generate revenue and keep customers happy.]
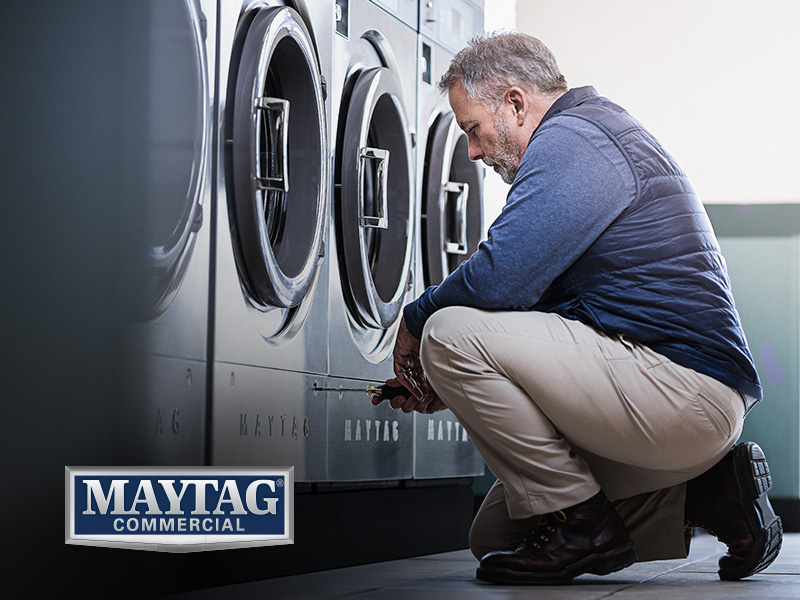
Most owners of laundromats with older washers and dryers eventually reach a point where they may begin to question the wisdom of continually investing their earnings in parts and repairs to keep those machines running – rather than using those funds to purchase new equipment with years of dependable service ahead.
Cutting such costs is one of the most significant factors owners must consider when retooling their facilities. In fact, according to a CLA Insights Report on equipment replacement, when laundromat owners were surveyed regarding the top 10 benefits of replacing washers and dryers, the benefit on which respondents most strongly agreed was “lowered expenses for parts and repairs.”
Reducing Repairs
Owners who retool their facilities with new washers and dryers can look forward to a reduction in recurring expenses for all of the replacement parts and service calls necessary to keep “perfectly good” older machines up and running. Moreover, the older the machines are, the greater the chance that replacement parts will be harder to obtain (or at least obtain quickly), resulting in even more downtime and lost revenues.
Although owners who do their own repairs might be able to reduce those costs somewhat, they also invest another limited commodity in their do-it-yourself efforts – their time. An operator who is handy at repairs often fails to put a monetary value on all of the time spent working on machines to keep them in working order – time that could be used more productively to attend to other business-related tasks, such as marketing or managing the business, or simply pursuing often-neglected personal activities.
Tapping Warranties
Another advantage of re-equipping is that new machines carry manufacturer warranties that reduce a laundromat’s exposure to any repair costs associated with those machines. By buying new equipment with warranties, an owner essentially “resets the clock” on service calls, repairs and parts.
This also means that, for the most part, fixed costs such as payments on a note and regular maintenance replace the variable costs of ad hoc repairs, maintenance and parts purchases, making it easier for the owner to stick to a budget.
Keeping the Wheels Turning
The most successful laundromat owners understand that the time always comes when there will be a diminished return on their original equipment investment. At that point, capital expenditures become necessary to maintain revenues, increase profitability and provide customers with the best possible experience.
New machines – because they run more consistently than older, repair-prone equipment – provide more uptime to generate revenue. They also offer greater programmability than older machines, enabling owners to increase revenues through such features as cycle modifiers, time-of-day pricing and multi-level vend for water temperature.
Increasing Customer Satisfaction
Looking beyond operational considerations, it’s also important for owners to consider customer needs and preferences when deciding to retool. Older machines may function well, but nonetheless seem ancient to customers – or too worn, too small or too slow compared to those of the competition.
There is also the simple fact that shiny new equipment looks like it’s worth the extra money to use. In other words, customers tend to be more open to price increases when they see better equipment and expanded functionality.
Savvy owners know that new equipment can boost customer satisfaction – and help their stores not only stand out against competitors, but also grow their customer bases. According to the CLA report cited above, 85 percent of laundromat owners either “agreed” or “strongly agreed” that customer satisfaction and retention are key benefits of equipment replacement – and 81 percent agreed that new machines attract more new customers.
In summary, it’s clear that parts and repair costs are often a key factor in an owner’s decision to replace equipment. The fact is that these expenses – and the other equipment-related factors explored in this series – will continue to rob laundromat owners of both time and money until the faulty equipment is traded out.