Improve Productivity by Embracing This Japanese PhilosophyYears ago, my good friend and fellow store owner Paul Pettefer and I began work on an employee manual. We wanted to create the best possible set of processes and procedures for our businesses and staff members.And, as Paul and I delved deeper into this project, it became my official indoctrination into the Japanese principle of Kaizen.Kaizen is less of a productivity “system” used to organize a to-do list and more of a philosophy. It’s a way of thinking and organizing everything – from the way you work to the way your team works together.Although Kaizen translates to “good change,” in productivity circles the term has come to mean “constant, continual improvement.” Put simply, every aspect of an organization should, at all times, strive to do what it does better. This philosophy first appeared shortly after World War II, when several Japanese businesses embraced the idea that doing things the way they’ve always been done was a bad idea.Inspired by Western competitors and manufacturing methods, Kaizen came to be synonymous with companywide efforts to intelligently streamline business practices and manufacturing methods, while simultaneously respecting the product, craft and people involved with making it.Today, many associate Kaizen with Toyota, which uses the philosophy as one of its core business principles. In fact, the auto manufacturer is so committed to continuous improvement that any worker on a Toyota assembly line can supposedly stop the line at any time to address a problem in production, correct an error, or suggest to management a better way to do things that reduce waste or improve efficiency.How do we apply Kaizen to our own businesses? This principle involves everyone within a company, from the CEO to the janitor. It looks at each one of their tasks, how they do them, and how those jobs can be made more efficient.The process begins by simply evaluating the task at hand. Take one task a day and evaluate it. Determine what that task is, what needs to be done and the basic elements of the task.The next step is to look for – and always be looking for – waste. In a past column, I discussed streamlining the wash-dry-fold process by eliminating any unnecessary, time-wasting steps. With production jobs, that’s what it comes down to – getting a stopwatch and figuring out how long it takes to process something. And then finding ways to do that job more efficiently.Can you create a work station for an employee who is processing something, in order to make the job easier? For example, if he or she is cleaning a restroom, perhaps create a cart with all of the tools needed to properly clean that restroom. What would that look like? What else can be done to improve that process?After you’ve done that, the next step is to do it again. After all, just because you’ve taken the first crack at it doesn’t mean you’ve created the best solution. What’s more, things change over time. This type of continuous improvement can be broken down into six steps:Standardize: Come up with a process for a specific activity that’s repeatable and organized.Measure: Examine whether the process is efficient using quantifiable data, like time to complete, hours spent, etc.Compare: Compare your measurements against your requirements. Does this process save time? Does it take too much time? Does it accomplish the desired result?Innovate: Search for better ways to do the same work or achieve the same result. Look for smarter, more efficient routes to the same end-goal that boost productivity.Standardize: Create repeatable, defined processes for those new, more efficient activities.Repeat: Go back to step one and start again.The key ingredient is the fact that those who are doing the work are the ones who need to help create the processes and be involved with their development. Leadership does nothing more than encourage involvement and engagement from the people who are impacted by the processes.At first, Kaizen may seem exhausting, but once it’s part of your mental approach to your work, your company and your team culture, it’ll feel natural. If you’re always looking for better ways to do things and always willing to give them a try, it’s just a step up to formalize it and make sure everyone’s on the same page.
Elite Strategic Corporate Allies
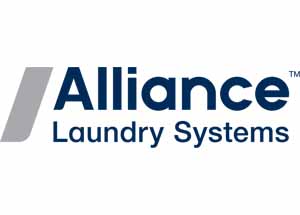
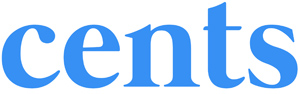
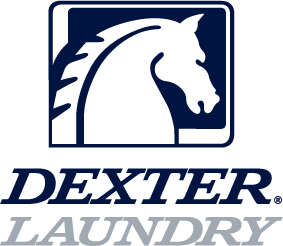
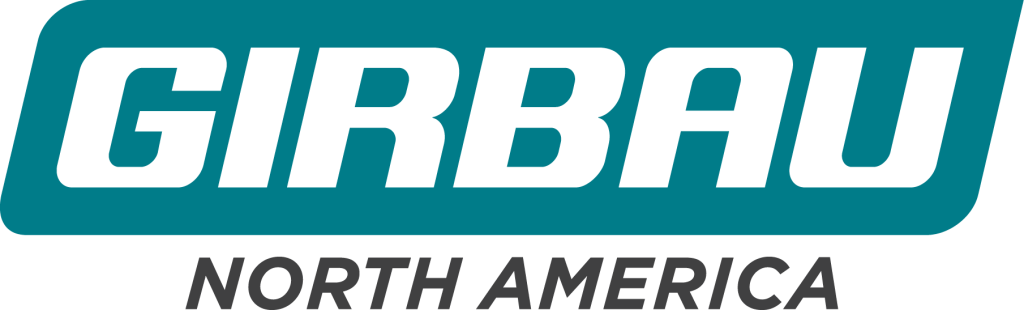
Premier Strategic Corporate Allies
CLA Business Solutions
CLA is working with select service providers to offer programs and services to help you with your business operations
New Laundromat Entrepreneur
Get this free guide to the laundry industry that will help you navigate your start-up. This is the definitive handbook from the CLA for potential investors interested in purchasing or building a laundromat.